5°/ Other rules to observe
The height between the infrastructure and the lower part of the LIMBEROLLER® center plate should be 10 to 30 mm larger than with conventional rollers.
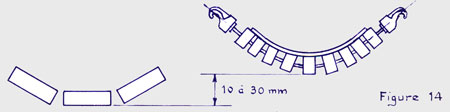
On most belt conveyors, the upper part of the motor drums is higher than that of the rollers. When using LIMBEROLLER®, the rollers must be lifted by placing shims under the supports.
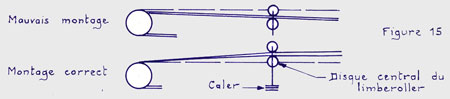
It is necessary to provide underneath the belt sufficient clearance to be able to clean and avoid the accumulation of materials which would quickly wear the neoprene wafers and put the LIMBEROLLER® out of service.
IMPORTANT :
In the case of a conveyor with a deep trough, for example, it is absolutely essential not to pass too rapidly from 0 ° (on reversing drum and motor drum) to 40 °, or by moving the first roller (1 , 50 to 2 m.), Preferably by placing an intermediate trough roll of about 20 ° between the drum and the LIMBEROLLER® at a trough of 40 °. By doing so, the roll is abnormally bent at the edges of the strip and the cable is broken in a very short period of time.
BELT OPERATIONS
It is always preferable for this junction to be made by gluing or by vulcanization. To be valid this work must be very well executed.
In the case where it is absolutely necessary to use a metal stapling, it must be able to perfectly fit the trough of the LIMBEROLLER® rollers without making any undulations. On the other hand, this stapling must have no projecting part.
If these two conditions are not realized, it will follow a rapid wear of the rolls of rollers.
|